(2-minute read)
Article Summary: Explores the fundamental ways opXR provides pivotal transformations for manufacturing.
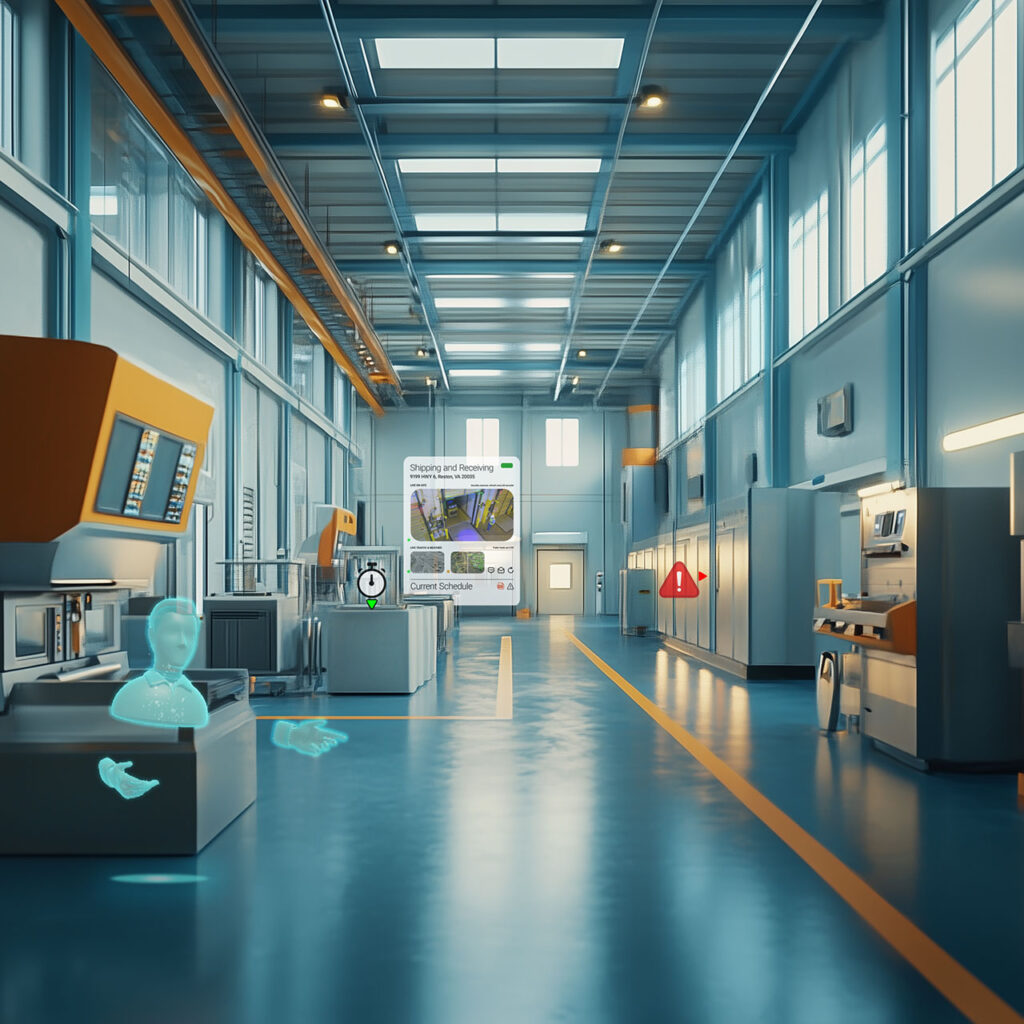
opXR is poised to provide a powerful digital transformation to the manufacturing industry by bridging the gap between the physical and digital worlds. It can connect with various manufacturing process elements, including machines, IoT sensors, fleet and asset trackers, people, and tasks.
By integrating with Human-Machine Interfaces (HMIs), XR can provide real-time data and visualizations directly to operators. This enables more efficient problem-solving, reduced downtime, and improved quality control. IoT sensors can be used to collect data on equipment performance and environmental conditions, which can then be displayed in an XR environment for analysis and optimization.
Fleet and asset trackers can be integrated with XR to provide real-time location information and track the movement of high value assets like equipment and materials. This can help to improve logistics, reduce waste, and optimize resource allocation. Additionally, XR can be used to connect people across different locations and departments, facilitating collaboration and knowledge sharing in real time. Additionally, having the ability to capture voice, movement, and gestures in recorded informal lessons or briefings allow teams to share information above and beyond standard emails and zoom calls.
As XR technology and digital transformation in general continue to advance with applications like opXR, manufacturing will become even more diverse and impactful. By leveraging XR, manufacturers can enhance efficiency, improve productivity, keep their employees safer, and drive innovation.